Surfing and reading articles in the world wide web, I recently came up to this article about flowmeters by The OMEGA website.
OMEGA is a well known industry in providing instrumentation solutions to various manufacturing firms.
As I 100 percent trusted this company with regards to instrumenation and controls, I would like to post here the said article. I have encountered various brands and models of flowmeters and all follow one principle in operation. Read on to feed to your brain.
INTRODUCTIONMagnetic flowmeters are low pressure drop, volumetric, liquid flow measuring devices. The low maintenance design–with no moving parts, high accuracy, linear analog outputs, insensitivity to specific gravity, viscosity, pressure and temperature, and the ability to measure a wide range of difficult-to meter fluids (such as corrosives, slurries and sludges)–differentiates this type of metering system from other flowmeters. Two basic styles of magnetic flowmeter are currently available from OMEGA Engineering:
1) Wafer-style, where highest accuracy (up to +0.5% of reading) measurements are required; and
2) Insertion-style, for greater economy and particularly for larger pipe sizes.
All OMEGA® magnetic flowmeters employ the state-of-the-art dc pulsed magnetic field system. The following discussion details the principle of operation, as well as the advantages, of dc pulsed type magnetic flowmeters.
PRINCIPLE OF OPERATIONFaraday’s LawThe operation of a magnetic flowmeter is based upon Faraday’s Law, which states that the voltage induced across any conductor as it moves at right angles through a magnetic field is proportional to the velocity of that conductor.
Faraday’s Formula:
E is proportional to V x B x D
where:
E = The voltage generated in a conductor
V = The velocity of the conductor
B = The magnetic field strength
D = The length of the conductor
To apply this principle to flow measurement with a magnetic flowmeter, it is necessary first to state that the fluid being measured must be electrically conductive for the Faraday principle to apply.
As applied to the design of magnetic flowmeters, Faraday’s Law indicates that signal voltage (E) is dependent on the average liquid velocity (V) the magnetic field strength (B) and the length of the conductor (D) (which in this instance is the distance between the electrodes).
In the case of wafer-style magnetic flowmeters, a magnetic field is established throughout the entire cross-section of the flow tube (Figure 1). If this magnetic field is considered as the measuring element of the magnetic flowmeter, it can be seen that the measuring element is exposed to the hydraulic conditions throughout the entire cross-section of the flowmeter. With insertion-style flowmeters, the magnetic field radiates outward from the inserted probe (Figure 2).

Figure 1: In-line magnetic flowmeter operating principle

Figure 2: Insertion-type flowmeter operating principle
MAGMETER SELECTIONThe characteristics of the fluid to be metered, the liquid flow parameters, and the environment of the meter are the determining factors in the selection of a particular type of flowmeter.
ConductivityElectrical conductivity is simply a way of expressing the ability of a liquid to conduct electricity. Just as copper wire is a better conductor than tin, some liquids are better conductors than others. However, of even greater importance is the fact that some liquids have little or no electrical conductivity (such as hydrocarbons and many nonaqueous solutions, which lack sufficient conductivity for use with magmeters). Conversely, most aqueous solutions are well suited for use with a magmeter. Depending on the individual flowmeter, the liquid conductivity must be above the minimum requirements specified. The conductivity of the liquid can change throughout process operations without adversely affecting meter performance, as long as it is homogeneous and does not drop below the minimum conductivity threshold. Several factors should be taken into consideration concerning liquids to be metered using magnetic flowmeters. Some of these are:
1. All water does not have the same conductivity. Water varies greatly in conductivity due to various ions present. The conductivity of “tap water” in Maine might be very different from that of “tap water” in Chicago.
2. Chemical and pharmaceutical companies often use deionized or distilled water, or other solutions which are not conductive enough for use with magnetic flowmeters.
3. Electrical conductivity is a function of temperature. However, conductivity does not vary in any set pattern for all liquids as temperature changes. Therefore, the temperature of the liquid being considered should always be known.
4. Electrical conductivity is a function of concentration. Therefore, the concentration of the solution should always be provided. However, avoid what normally is a logical assumption, such as: That electrical conductivity increases as concentration increases. This is true up to a point in some solutions, but then reverses. For example, the electrical conductivity of aqueous solutions of acetic acid increases as concentration rises up to 20%, but then shows a decrease with increased concentration to the extent that, at some concentration above 99%, it falls below the minimum requirement.
Acid/CausticsThe chemical composition of the liquid slurry to be metered will be a determining factor in selecting the flowmeter with the proper design and construction. Operating experience is the best guide to selection of liner and electrode materials, especially in industrial applications, because, in many cases, a process liquid or slurry will be called by a generic name, even though it may contain other substances which affect its corrosion characteristics. Commonly available corrosion guides may also prove helpful in selecting the proper materials of construction.
VelocityThe maximum (full scale) liquid velocity must be within the specified flow range of the meter for proper operation. The velocity through the flowhead can be controlled by properly sizing the meter. It isn’t necessary that the flowhead be the same line size, as long as such sizing does not conflict with other system design parameters. Although the meter will increase hydraulic head loss when sized smaller than the line size (because the meter is both obstructionless and of short lay length), the amount of increase in head loss is negligible in most applications. The amount of head loss increase can be further limited by using concentric reducers and expanders at the pipe size transitions. As a rule of thumb, meters should be sized no smaller than one-half of the line size. Because of the wide rangeability of magnetic flowmeters, it is almost never necessary to oversize a meter to handle future flow requirements. When future flow requirements are known to be significantly higher than start-up flow rates, it is imperative that the initial flows be sufficiently high and that the pipeline remain full under normal flow conditions.
Abrasive SlurriesMildly abrasive slurries can be handled by magnetic flowmeters without problems, provided consideration is given to the abrasiveness of the solids and the concentration of the solids in the slurry. The abrasiveness of a slurry will affect the selection of the construction materials and the use of protective orifices. Abrasive slurries should be metered at 6 ft/sec or less in order to minimize flowmeter abrasion damage. Velocities should not be allowed to fall much below 4 ft/sec, since any solids will tend to settle out. An ideal slurry installation would have the meter in a vertical position. This would assure uniform distribution of the solids and avoid having solids settle in the flow tube during no-flow periods. Consideration should also be given to use of a protective orifice on the upstream end of a wafer-style magnetic flowmeter to prevent excessive erosion of the liner. This is especially true since Tefzel liner have excellent chemical resistance, but poor resistance to abrasion. In lined or non-conductive piping systems, the upstream protective orifice can also serve as a grounding ring.
Sludges and Grease-Bearing LiquidsSludges and grease-bearing liquids should be operated at higher velocities, about 6 ft/sec minimum, in order to reduce the coating tendencies of the material.
ViscosityViscosity does not directly affect the operation of magnetic flowmeters, but, in highly viscous fluids, the size should be kept as large as possible to avoid excessive pressure drop across the meter.
TemperatureThe liquid’s temperature is generally not a problem, providing it remains within the mechanism’s operating limits. The only other temperature considerations would be in the case of liquids with low conductivities (below around 3 micromhos per centimeter) which are subject to wide temperature excursions. Since most liquids exhibit a positive temperature coefficient of conductivity, the liquid’s minimum conductivity must be determined at the lower temperature extreme.
Advantages of the DC Pulse StyleFrom the principles of operation, it can be seen that a magnetic flowmeter relies on the voltage generated by the flow of a conductive liquid through its magnetic field for a direct indication of the velocity of the liquid or slurry being metered. The integrity of this low-level voltage signal (typically measured in hundreds of microvolts) must be preserved so as to maintain the high accuracy specification of magnetic flowmeters in industrial environments. The superiority of the dc pulse over the traditional ac magnetic meters in preserving signal integrity can be demonstrated as follows:
QuadratureSome magnetic flowmeters employ alternating current to excite the magnetic field coils which generate the magnetic field of the flowmeter (ac magnetic flowmeters). As a result, the direction of the magnetic field alternates at line frequency, i.e., 50 to 60 times per second. If a loop of conductive wire is located in a magnetic field, a voltage will be generated in that loop of wire. From physics, we can determine that this voltage is 90° out of phase with respect to the primary magnetic field. The magnitude of this error signal is a function of the number of turns in the loop, and the change in magnetic flux per unit time. In a magnetic flowmeter, the electrode wires and the path through the conductive liquid between the electrodes represent a single turn loop. The flow-dependent voltage is in phase with the changing magnetic field; however, flow independent voltage is also generated, which is 90°out of phase with the changing magnetic field. The flow-independent voltage is therefore an error voltage which is 90° out of phase with the desired signal. This error voltage is often referred to as quadrature. In order to minimize the amount of quadrature generated, the electrode wires must be arranged so that they are parallel with the lines of flux of the magnetic field. In ac field magmeters, because the magnetic field alternates continuously at line frequency, quadrature is significant. It is necessary to employ phase sensitive circuitry to detect and reject quadrature. It is this circuitry which makes the ac magnetic meter highly sensitive to coating on the electrodes. Since coatings cause a phase shift in the voltage signal, phase-sensitive circuitry leads to rejection of the true voltage flow signal, thus leading to error. Since dc pulse magmeters are not sensitive to phase shift and require no phase-sensitive circuitry, coatings on the electrodes have a very limited effect on flowmeter performance.
WiringIn ac magnetic flowmeters, the signal generated by flow through the meter is at line frequency. This makes these meters susceptible to noise pickup from any ac lines. Therefore, complicated wiring systems are typically required to isolate the ac flowmeter signal lines from both its own and from any other nearby power lines, in order to preserve signal integrity. In comparison, dc pulse magmeters have a pulse frequency much lower (typically 5 to 10% of ac line frequency) than ac meters. This lower frequency eliminates noise pickup from nearby ac lines, allowing power and signal lines to be run in the same conduit and thus simplifying wiring. Wiring is further simplified by the use of integral signal conditioners to provide voltage and current outputs. No separate wiring to the signal conditioners is required.
PowerBy design, ac magnetic flowmeters typically have high power requirements, owing to the fact that the magnetic field is constantly being powered. Because of the pulsed nature of the dc pulse magmeter, power is supplied intermittently to the magnetic field coil. This greatly reduces both power requirements and heating of the electronic circuitry, extending the life of the instrument.

Figure 3: Vertical installation of inline meter
Auto-ZeroIn traditional ac magnetic flowmeters, it is necessary after installation of the meter to “null” or “zero” the unit. This is accomplished by manual adjustment which requires that the flowmeter be filled with process liquid in a no-flow condition. Any signal present under full pipe, no-flow conditions is considered to be an error signal. The ac field magmeter is therefore “nulled” to eliminate the impact of these error signals. In the case of OMEGA® FMG-400 Series Magmeters, automatic zeroing circuitry has been included to eliminate the need for manual zeroing. When the magnetic field strength is zero between pulses, the voltage output from the electrodes is measured. If any voltage is measured during this period, it is considered extraneous noise in the system and is subtracted from the signal voltage generated when the magnetic field is on. This feature insures high accuracy, even in electrically noisy industrial environments.
InstallationOMEGA® magnetic flowmeters are designed for easy installation. FMG-400 Series Magmeters are ideal substitutes for the flanged spool type meter, which are heavier and significantly more expensive. The thin wafer style of the FMG-400 Series allows them to be slipped between standard flanges, without the need to cut away pipe to make room for the meter. Furthermore, the low weight of the meter means that, in many cases, no additional pipe supports are required after meter installation. Recommended piping configurations include the installation of by-pass piping, cleanout tees and isolation valves around the flowmeter (Figures 3 and 4). With insertion-style magmeters, even greater reductions in weight and cost have been achieved. Installation is accomplished by threading the piping system into the tee fitting supplied with the meter, or by drilling a tap into the line to accept the fitting that comes with the meter. Prior to installation of the meter, the following recommendations and items of general information should be considered. First, before installing a magmeter, it is important to consider location. Stray electromagnetic or electrostatic fields of high intensity may cause disturbances in normal operation. For this reason, it is desirable to locate the meter away from large electric motors, transformers, communications equipment, etc., whenever possible. Second, for proper and accurate operation, it is necessary that the flowmeter be installed so that the pipe will be full of the process liquid under all operating conditions. When the meter is only partially filled, even though the electrodes are covered, an inaccurate measurement will result. Third, for magnetic flowmeters, grounding is required to eliminate stray current and voltage which may be transmitted through the piping system, through the process liquid, or can arise by induction from electromagnetic fields in the same area as the magmeter. Grounding is achieved by connecting the piping system and the flowmeter to a proper earth ground system. Unfortunately, this is not always done properly, resulting in unsatisfactory meter performance. In conductive piping systems, a “third wire” safety ground to the power supply and a conductive path between the meter and the piping flanges are typically all that is required. In non-conductive or lined piping systems, a protective grounding orifice must be supplied to provide access to the potential of the liquid being metered. Dedicated or sophisticated grounding systems are not normally required. Detailed information concerning proper flowmeter grounding is provided with the owner’s manual that comes with each flowmeter. Finally, the position of the flowtube in relation to other devices in the system is also important in assuring system accuracy. Tees, elbows, valves, etc., should be placed at least 10 upstream and 5 downstream pipe diameters away from the meter to minimize any obstructions or flow disturbances.
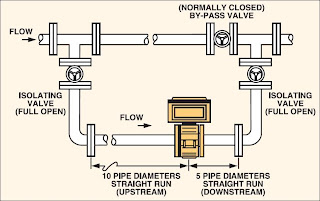
Figure 4: Horizontal installation of in-line meter
Technical texts courtesy of Omega.